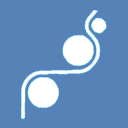
FLEXO PRINTING
Within the printing industry, flexo printing is one of the fastest developing areas. To 20 years ago it would have been impossible to imagine that either offset or mélynyomtatással having to compete, now we can say that the technology is very good value for money. The benefits of flexo-printing are recognized on an international level, so our outside Hungary produces a variety of sizes, packaging materials use, for a number of European partners.\r\n\r\nThe 5 most important advantages of flexo-printing: High quality prints, which is associated with excellent price. Átszerelhetőség.Nagy fast print speeds. Short settling time. a wide spectrum of print media (eg. paper, aluminum, műanyagtársítások). The flexo-printing technology of flexo-printing with high print a special area where the printing form a flexible photopolymer plates (see production preparation). Based on three different types of construction machinery in the flexographic printing. The first arrangement of cylinders by: individual counter-pressure cylinder printing machines, cabinets line constructed flexonyomdagépek principle, central impression cylinder flexonyomdagépek. 2. Toner Works by: dip rubber cylinder flexonyomdagépek, chamber doctor blade flexonyomdagépek. 3. Paint Type: flexonyomdagépek water-based, solvent-flexonyomdagépek, UV flexonyomdagépek. Compared to established technologies, flexographic printing within the requirements of the age correspond to the central impression cylinder chamber doctor blade presses without gear drives. Our company has 2 central impression cylinder has a gearless flexonyomdagéppel. These six or eight colorful.
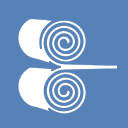
LAMINATION
In the plastic packaging material industry it was a huge development, when the lamination became more prevalent. 20 years ago, it was hard to find a good looking laminated product, but nowadays they suit for the aesthetic demand. Even more important, the physical and chemical development of the packaging material! With the use of the laminated materials the scale of unit weight can be lower, but the quality keeping time is longer.
Krajcár company purchased an eco-friendly, high technology lamination machine in 2016. With this machine we are able to produce 2-3 or 4 layered packaging material, so we can fulfill the customer’s needs. We also have a smaller, solvent free lamination machine.
Technologies we use during the lamination:
- solvent based
- water based
- solvent free: one component glue and two components glue
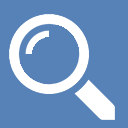
GRAPHICAL PREPARATION AND PRINTING
During the prepress we making Your graphic to printable. Our colleagues processes the graphic, they are divide to colors and make the transformations which are required to flexo printing. Before the print plates we sending first a digital pdf from the graphic in composite ans separate format, and a color printed proof to approval. After the approvals we are producing the print plates. The preparation time from the graphic to the plates is approx. 1-2 weeks.
Create all text in artwork in "outlines", or attached the font files. All Photoshop image files should be linked and attached, the resolution of photographic image files must be no less than 300 dpi. Create the images with CMYK colour mode. In each case we asking to a preview pdf format.
If you are going to use a spot colour please reference the Pantone ( PMS #). In the absence of this, we will propose appropriate colors. If You have a reference or other sample (proof, color print, sample from the previous production) please be kind to send it to us.
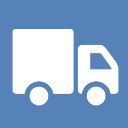
DELIVERY
We deliver our products with our own cars, or with our contracted forwarder company.
We can help to arrange not only the internal deliveries, but the custom process as well.
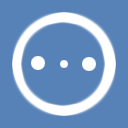
PERFORATION
There are special fields, like fruit packaging, where the natural ventilation of the product is necessary. During the macro perforation, 5-8 mm diameter holes are produced on optional places on the foil, so in this way the products will stay fresh. It is possible the positioning of the holes to the graphic on printed foils. During the micro perforation, the production of 0,8-2 mm diameter holes are possible. These kinds of films are produced mainly for bakery products.
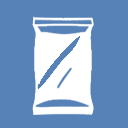
POUCH PRODUCTION, CONFECTION
One of the most important parts of our production is the pouch production. According to our customer’s needs, we produce pouches in different styles with different materials.
These are the types of the pouches:
- Pillow pouches made from PE tube. These are cost effective, but not so up-to-date.
- Side sealed pillow pouches made from duplex or triplex laminated foil. Types: with round hole, EURO hole, sponge handle, zipper, tear notch, with zipper but open from the bottom of the pouch. Possible sizes: width 30 mm-400 mm, length 75 mm-600 mm
- Stand up pouch: made from different laminated foils, in different styles. We have several tools for the bottom sealing, we can produce them in different sizes and styles.
- Pouch with cap and spout: made from different laminated foils, can be pillow pouch or stand up pouch. We have the possibility, to deliver the pouches on rails. The cap and spout can be find on the top of the pouch or on one side of the pouch.